Volumetric instruments
Better technology, more efficiency
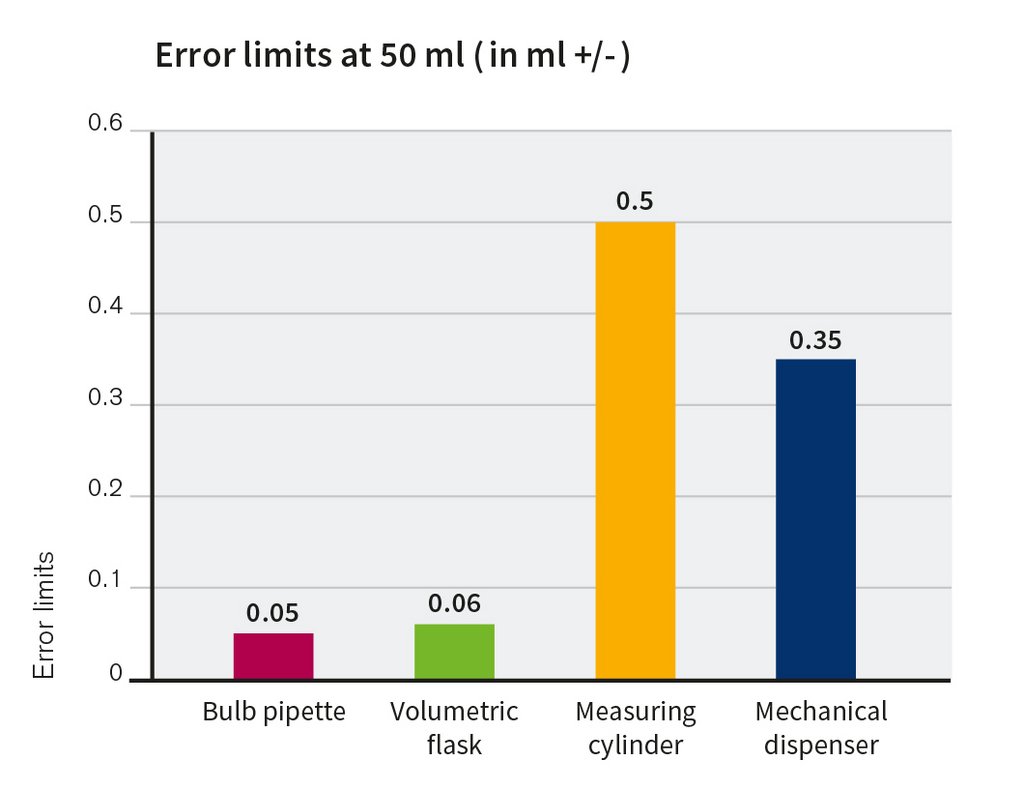
But where do today’s volumetric instruments really stand in terms of precision and efficiency? The 50th anniversary of the BLAUBRAND® brand is the perfect occasion to take a look at the current state of the technology.
Today’s bottletop dispensers, micropipettes and other mechanical liquid handling devices offer efficient dispensing alternatives. However, in terms of accuracy, class A or AS volumetric flasks and bulb pipettes have been the cream of the crop for 50 years. The small diameter at the ring mark enables pinpoint adjustments and readings. Internationally recognized standards, such as DIN EN ISO 1042 (volumetric flasks) or DIN EN ISO 648 (bulb pipettes), guarantee the fundamental qualities of volumetric instruments, but only provide a basis.
In reality, error limits are only as relevant as the accuracy actually read. And a lot has changed in that regard. The ring mark and inscriptions on BLAUBRAND® products are printed in the eponymous blue because this color has a high contrast, making it very easy to read. The blue color is an enamel paint that is fired into the glass at temperatures between 400° C to 550° C, depending on the glass type. As a result, it is resistant to aggressive cleaning agents and – depending on the wash program – its readability is still excellent after several hundred wash cycles. This not only simplifies precision readings, but also extends the life of the instrument and reduces resource consumption.
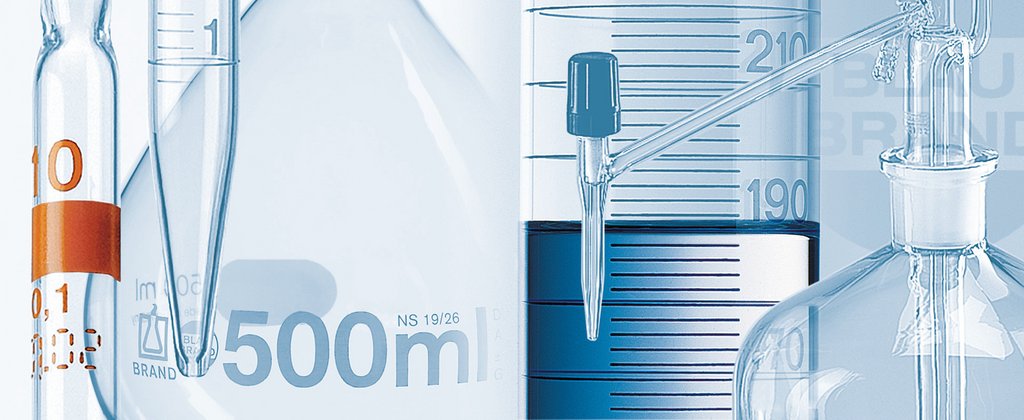
Minimizing the risk of breakage is another aspect that has seen considerable improvements. The key to durability is not so much the thickness of the glass, but rather the elimination of stress on the glass. Blank glassware is put under stress during the manufacturing process, which can lead to breakage under mechanical or thermal load. Therefore, BLAUBRAND® volumetric instruments undergo a temperature-controlled process, which eliminates the stress by exposing the blank glassware to controlled heating and cooling over several hours. This is required to achieve the best possible mechanical strength and to maintain a constant volume when the glass is exposed to subsequent thermal loads. As a result, BLAUBRAND® volumetric instruments can be heated up to 250° C in a drying cabinet or sterilizer. Uneven heating or sudden temperature changes should be avoided if possible.
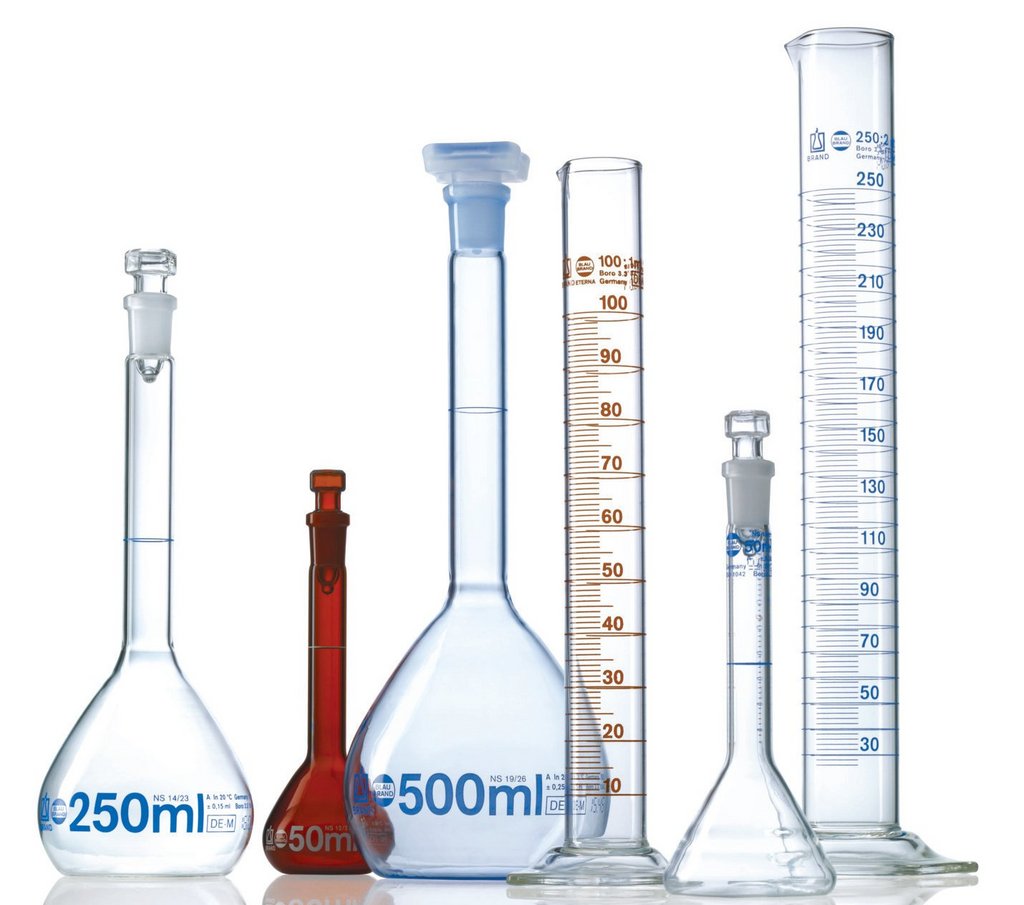
Certificates and documentation play an increasingly important role in today’s regulated laboratory environment. Certification processes have also evolved. Factory test certificates, as batch or individual certificates, are now standard with every delivery. In addition, individual certificates are available which refer to the individual serial number. In laboratory analysis, and especially in the pharmaceutical industry, many laboratories are accredited and therefore work with measuring equipment that has also been calibrated in an accredited laboratory. For these laboratories, BRAND® also offers DAkkS calibration certificates through its accredited DAkkS calibration laboratory.
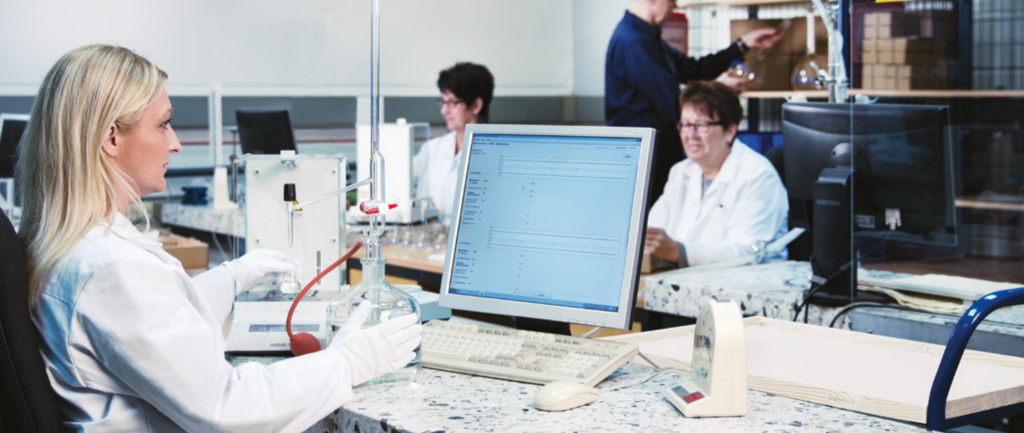
Quality management at BRAND begins in the product planning phase and follows its development up to series production. Constant testing during the entire production process supports the goal of producing volumetric instruments with the smallest possible deviation from the nominal value (accuracy) and narrow scatter of the individual values (coefficient of variation). The last step of this Statistical Process Control (SPC) is testing a random sample of the finished product during final inspection according to DIN ISO 3951. The quality management system applied at BRAND and certified to DIN EN ISO 9001 is a combination of process monitoring and random checks.
Optimized production processes reduce production-related fluctuations and deviations to a minimum. The accepted quality level (AQL) is at least 0.4. This means that the defined limits are met with a statistical certainty of at least 99.6%.
High precision, long-term readability of inscriptions, mechanical durability and compliance with regulatory requirements have made BLAUBRAND® volumetric instruments a reliable and resource-saving lab partner for 50 years.
BRAND – simple, easy and efficient!